
What is variable durometer braided tubing?
Variable durometer braided tubing is a catheter shaft which incorporates more than one material hardness over the length of the tube, while encapsulating a metal or polymer braided structure in the wall.
Medical applications employing braid-reinforced catheters often require a stronger durometer (hardness) at the proximal end than at the distal tip. The conventional method is to change the durometer with discrete assemblies of different durometers.
Putnam Plastic’s braided TIE™ technology eliminates the traditional manual approach with a proprietary, continuous processing method to create a fully integrated composite shaft. These shafts incorporate the traditional three-layer approach with some modifications to improve performance and reliability.
What are the advantages of Putnam’s braided plastic extrusions?
Braided catheters with multi-durometer outer layers for variable flexibility have traditionally been manually assembled from discrete components and heated to create the final component. This is costly and presents challenges for validating a highly manual manufacturing process. Product performance can also vary due to poor bonding between the layers and at the interface of the discrete segments on the outer layer, where hinge points occur.
Braided TIE™ shaft manufacturing rethinks the conventional approach to achieve a more integrated and reliable component, at a lower cost.
How is a variable braided tube extrusion formed?
Putnam Plastics has the ability to produce variable braid patterns over the length of a shaft. This technology allows engineers to transition pic angles from the proximal to distal end. When the variable braid is encapsulated between the outer/inner polymer layers, the performance characteristics can be altered significantly. This allows for a wide range of catheter customization.
What medical devices, body parts or procedures is Braided TIE™ technology commonly used in?
Braided TIE™ tubing is a design option for any catheter requiring a stiffer proximal, soft distal, and the need to transmit torque. It is commonly used in a variety of micro catheters and delivery systems. Talking with a sales representative is the best way to discuss your many options.
What ISO certification does Putnam Plastics have?
Putnam’s leading-edge custom tubing manufacturing facility is ISO 13485:2016 certified. Our dedicated clean room space is ISO compliant, so you get your most challenging specifications met—with good speed to market and competitive rates.
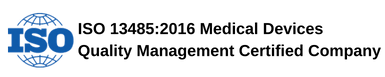
Why is Putnam the best choice for this product?
Putnam Plastics invented, and patented the variable durometer extrusion technology known as TIE. For over 30 years, tooling advancements have been made to widen the scope of applications. It is now used in single lumens, braids, coils, multi lumens and tapered shafts.