For full contract manufacturing needs, visit our sister company: Putnam Medical
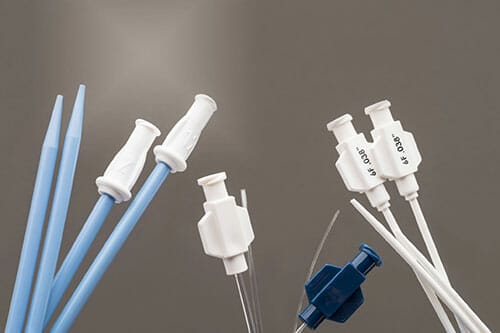
How does Putnam assist you during the research and development phase?
We offer our extensive knowledge base and work to provide a solution to our customers’ needs including but not limited to material research, design and specification recommendations. Our large groups of engineers, who collaborate on all projects, bring many decades of experience and knowledge to your specific project.
What types of testing does Putnam do during the assembly development phase?
- Putnam provides customer-specified mechanical testing such as burst testing, tensile and elongation, and torque testing to name just a few.
- We also have SPC capability and CPK or statistical analysis for product realization.
What types of catheter assemblies can Putnam configure?
With the addition of our in-house finishing facility, we can manufacture complete catheter assemblies from start to finish—all under one roof. For example:
- Device used for In Vitro Fertilization (IVF) procedures: This assembly is comprised of three components. The inner component is a variable durometer polyurethane TIE™ tube, which is insert molded, printed, and RF tipped. The outer sheath is a tri-layer tube, which is also tipped, printed, and insert molded. Together they allow for optimal lubricity as well as shapeability. This complete assembly is packaged in a profile protective tube, specifically designed to lock in place with the inner components for optimal fit and security.
- Catheter used in a Central Venous Access Catheter (CVAC) for the infusion of therapeutic drugs: The main shaft is a dual lumen extrusion, with two extension tubes, a strain relief, and two hubs on the proximal end. The distal portion of the tube was formed into a helical coil profile, with 11 holes at .003” diameter each. The distal tip transitioned the dual lumen to a single lumen through laser sealing.
What experience does Putnam Plastics have in providing innovative solutions to clients’ challenges?
Putnam finds solutions—even if it means pioneering a new technology
The concern: A customer worried about the possibility of a dilator falling out of its sheath during procedure, yet wanted to maintain a soft durometer on the distal end. The result: Putnam’s patented TIE™ tubing technology was used to provide a soft distal tip, that does not cause damage during the procedure—while eliminating the physician’s worry of the tube sliding out due to a stiffer proximal end.
Putnam solves issues—before they become a problem
The issue: A client’s drug delivery system employed some fragile parts—that necessitated some additional preparation. The finished component involved an extremely small diameter, tapered polyimide tube along with 14 laser-drilled holes, and a robotically bonded metal hub.
The solution: Due to how delicate the parts are, our engineers designed and built custom packaging to ship and store the delivery system safely.
What are steps in the medical device development process at Putnam?
- RFQ (Request for Quote),
- engineering review,
- tooling and engineering design & development,
- prototype fabrication,
- product realization and validation, and
- large scale manufacturing
How does Putnam support faster speed to market of prototypes for you?
Not only do we have a dedicated R&D team with R&D tool design and tool room, but we continually invest in engineering resources and equipment to build capacity and reduce lead times—so you get quality products faster.
Which medical devices can Putnam provide rapid prototyping for?
Putnam offers custom rapid prototyping for a range of minimally invasive devices for cardiovascular, neurovascular and endovascular specialties
What advantages does Putnam’s large scale production service give you?
When partnering with Putnam, you get high-quality custom devices, extensive engineering support, and the ability to expand production quickly with our new, large manufacturing facility.
What benefits does working with Putnam from design through to full manufacturing process bring you?
- We thrive on generating high-end challenging products—that other manufacturers shy away from.
- With turnkey solutions, engineering expertise, and our ability to provide very challenging components that our competitors cannot, you receive top-notch medical device assembly.
- Our end-to-end device assembly allows us to reduce costs through new technologies. We research and develop tubing advancements that change labor-intensive products into sleeker processes, but have the space to offer full reflow and hand lay-up capabilities when it makes sense.
- For decades, partners around the world have been consulting with us for innovative solutions to their tubing questions. How can we put our expertise to work for you?