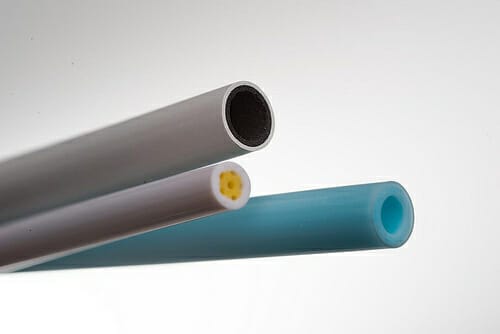
What is a coextruded medical tube?
Coextrusion technology improves functionality by applying unique materials, with their associated properties, in the desired location of the coextruded tube. For example, lubricious materials can be extruded on the inner diameter of a tube while a soft, flexible material is simultaneously extruded on the outside diameter.
Coextrusion is often associated with the extrusion of multiple (two or more) layers of material extruded simultaneously to produce a multilayered medical tube. Coextrusion may also include extrusion of a radiopaque polymer stripe along the wall, intermittent extrusion of distinct polymers along the length and various other combinations in which two or more materials are extruded into a single tube construction. Coextrusion is invaluable for lean manufacturing of components that would otherwise require assembly of distinct parts.
What materials can be coextruded and what are the benefits?
Because Putnam Plastics has two- and three-layer technology, as well as continuous and discrete processing, the material combinations for a multi-layered tube are almost infinite. Talking with a sales representative is the best way to discuss your material options.
What options should you keep in mind when procuring multi-layered medical tubing?
When choosing materials for a coextruded tube, material compatibility is important. Some material combinations create a molecular bond, while others generate a mechanical bond. Putnam offers the widest range of dimensional and material combinations.
How many layers can be coextruded together?
Our cutting-edge manufacturing facility can produce 2, 3, 4, 5, 6 and 7-layer material structures—to give you the most best blend of material attributes.
Can multiple lumens be coextruded together?
Yes, multi-lumens can be coextruded in a variety of designs and configurations to give you the best performing tube for your medical application.
What other coextruded tubing options does Putnam Plastics offer?
- Stripes can be created to assist medical personnel in identifying different catheters.
- A radiopaque layer can be added so physicians can determine, under fluoroscopy, where in the patient’s body the catheter is.
- Different layers can provide different beneficial attributes such as a soft, slippery outer layer to ease insertion, combined with a firmer inside liner to allow a guide wire to travel smoothly through the tube.
- Adding a permeable-resistant layer that won’t degrade from certain chemicals can help maintain the functionality of a semi-permanent catheter over the long-term.
Why would you choose this type of extrusion technology over others?
The ability to create an extrusion with different internal and external materials provides you with a catheter shaft with unique properties that cannot be achieved by one material. A shaft can be custom designed to give you more options:
- improved lubricity
- added flexibility
- compatible bonding or printing surfaces
- moisture or vapor barriers
- increased torque and column strength.
What medical devices, body parts or procedures is coextruded tubing commonly used in?
Coextruded and multi-layer shafts can be found in all types of catheter designs that require unique performance characteristics, to name just a few fields:
- cardiology, for example, a coextruded tube can provide a lubricious inner lining for a guide wire to smoothly travel through during a percutaneous transluminal coronary angioplasty (PTCA),
- neurology,
- oncology, and
- interventional radiology.
What ISO certifications is Putnam Plastics equipped to comply with?
Our state-of-the-art medical manufacturing facility is ISO 13485:2016 certified. Putnam’s skilled staff can produce coextrusion prototypes through to full production in our dedicated clean manufacturing space within our 37,000 square foot (3431.4 square meters) facility.
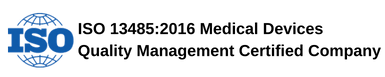
Why is Putnam the best choice for coextruded medical tubing?
- Putnam Plastics has over 40 years of experience assisting medical device companies design and develop first-ever catheter tubing. With the widest range of materials and capabilities, Putnam has become a solution provider for extrusion challenges—with excellent results.
- As specialists in high-tech extrusion, we have all our operations in-house to control the process and to give you better speed-to-market. To speak with a Putnam engineer or sales representative about your multi-layered medical tubing needs, click below.