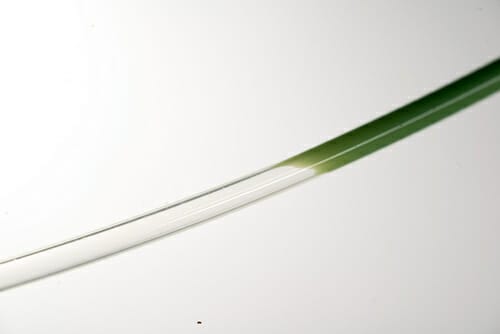
What is Total Intermittent Extrusion (TIE™)?
Total Intermittent Extrusion (TIE™) is a proprietary process capable of producing extrusions with variable durometers along their length. This innovative technology is commonly used in composite catheter shafts to provide a soft tip or a combination of flexibility and stiffness for insertion. In many cases, TIE™ extrusions are used to replace manually assembled composite shaft constructions (i.e. hand layups).
What materials can be used in an intermittent extrusion?
- Pebax®
- Polyurethane
- Polyethylene
- Polyester
What kind of features does composite medical tubing offer?
Choosing Putnam’s TIE™ process gives you a wide range of medical tubing choices:
- Most any color combinations can be used
- Round and profile shapes are possible
- Sizes range from less than 0.0393” ODs to greater than 0.0787” ODs
- Common tolerances range from +/-.0005” to +/-.002”
- A lubricious ID is available
- A wide range of possible multi lumen designs
- Variable pic braids and coils
What other intermittent plastics extrusion options does Putnam Plastics provide?
Putnam Plastics also has the ability to create intermittent extrusions through the lay-up process. This process allows for immediate material transitions, the ability to incorporate marker bands under the outer layer, and is sometimes a good option for small evaluation runs.
Why would you choose this type of medical tubing extrusion technology over others?
Manual assembly of multiple tube components of variable durometers over a mandrel and bonding for a continuous shaft is time consuming and inherently expensive. Bonds between the segments are very dependent upon the flow characteristics of the polymer, which vary from lot to lot.
Replacing two or more subcomponents of a lay up assembly with a single TIE extrusion addresses both of these concerns. First, one tubing component replaces two or more, reducing the labor required to build the assembly and eliminating opportunities for the segments to be misaligned. Second, the TIE extrusion eliminates one or more bonds from the layup assembly, eliminating a possible failure point. Third, the TIE process can be validated and is less susceptible to lot-to-lot variations in raw material.
What medical devices is this commonly used in?
Total intermittent extrusions are commonly used in PICC line tubing manufacture.
What ISO certifications is Putnam equipped to comply with?
Our custom tubing manufacturing center is ISO 13485:2016 certified. We also have a designated ISO-compliant clean room to meet stringent regulatory controls.
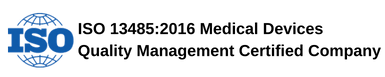
Why is Putnam Plastics the best choice for variable durometer tubing?
Putnam Plastics pioneered variable durometer continuous extrusion technology. Over the past 20+ years, we have incorporated this technology into multi-lumen, taper, and braided shafts.
Our three decades of experience as a material science innovator means you can rely on Putnam for excellence and dependability. To speak with a Putnam engineer or sales representative about your custom variable durometer tubing needs, click below.