DAYVILLE, CT USA – (September 11, 2012) – Putnam Plastics Corporation, a leader in advanced extrusion for minimally invasive medical devices, has added variable pitch braid and coil reinforcement to its portfolio of variable flexibility medical catheter shaft technologies. These continuous manufacturing technologies are designed to reduce cost and improve product performance of complex shafts traditionally assembled manually. Variable braiding or coiling can also be used in conjunction with geometric tapering or sequential polymer extrusion of distinct materials to enhance pushability and torque of catheters while maintaining flexibility to navigate vascular pathways deeper in the body.
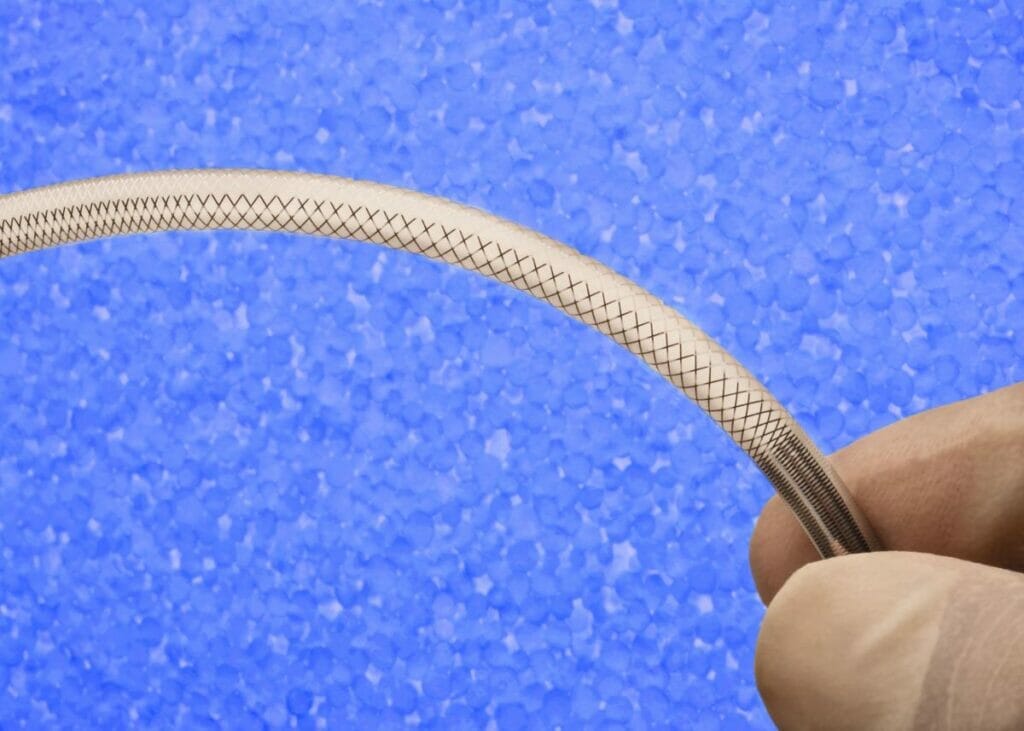
Today’s vascular procedures are reaching further into the body with longer, thinner catheters. While enhanced rigidity at the proximal end is required for pushability and torque of these catheters without kinking or buckling, the distal end must remain flexible to navigate complex vascular pathways. Traditional manual assembly of shaft segments with varying flexibility can be costly and performance can be compromised in bonded regions or at the union of the segments. Putnam’s Plastics portfolio of variable flexibility shaft technologies are designed to eliminate assembly labor costs with continuous manufacturing methods and improve product performance by eliminating weak or abrupt bonded joints in manual assemblies.
Putnam’s variable wire reinforcement technology includes variable wire coiling for improved kink resistance and variable braiding for improved torque performance. Reinforcement wires include stainless steel, nitinol (nickel titanium) and copper that are incorporated into extruded tubing ranging from 0.010 to 0.450 in. (0.025 to 1.143cm) in diameter. Reinforcing coils can transition from complete coverage up to 5 wraps/in. (1.97 wraps/cm), and braided wires can transition from complete coverage up to approximately 1 pick/in. (0.39 picks/cm).
“Variable wire reinforcement is known to provide unique performance attributes along the catheter shaft,” said Larry Alpert, Product Development and Technology Manager at Putnam. “By combining this with other continuous manufacturing technologies, such as sequential polymer extrusion or geometric tapering, we are able to provide highly tailored shaft performance while eliminating manual labor costs associated with hand layup assemblies.”