DAYVILLE, CT, USA – (October 3, 2013) – Putnam Plastics Corporation, a leader in advanced extrusion for minimally invasive medical devices, reports increased interest in integrated catheter components made by medical device companies. These components leverage continuous manufacturing to combine sub-component processes, eliminate assembly steps and reduce manual labor, thus allowing device companies to reduce overall costs.
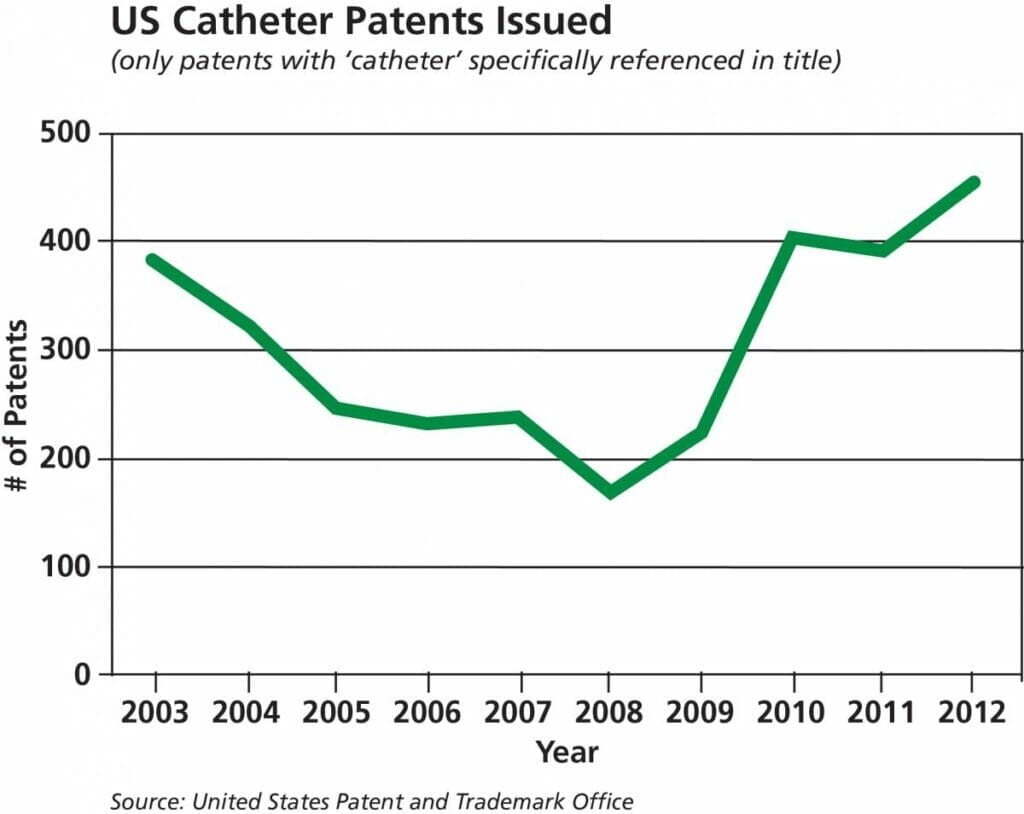
“Industry reports in 2009 suggested double digit compound annual growth rates for the interventional cardiology devices. By 2012 some industry reports adjusted this growth rate down into the single digits,” said Jim Dandeneau, Putnam Plastics Chief Executive Officer. “However, this more likely reflects competitiveness and cost reduction pressures on devices rather than decreased innovation.” Over a ten year period beginning in 2003 there was a steady decline in these patents issued until 2008, where it bottomed out at 168. Since then, there has been a strong increase in catheter patents issued reaching 454 in 2012, representing a 170% increase over the four year period.
“At Putnam Plastics, we have experienced double digit demand in complex catheter shafts since 2008,” continued Dandeneau. “Leading device companies are increasingly looking for innovative manufacturing solutions to produce better catheter shafts while reducing total production costs and time to market.”
Putnam Plastics’ growth of ‘continuous manufacturing technologies’ for complex catheter shafts continues to exceed market growth rates. Continuous manufacturing integrates multiple extrusion related processes to produce tubing with different properties on the inside and outside surfaces, and variable stiffness from the proximal to distal ends. These technologies replace costly manual assembly of discrete components for angioplasty, angiography, guiding and other interventional catheters.