Why would you choose polyimide shaft liners for catheter tubing?
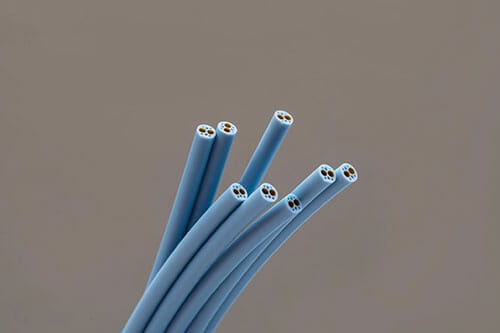
Due to its ability to be produced in very thin walls and its high tensile properties, polyimide lumen liners are ideal for catheters that must resist high pressure without dramatically altering the feel and performance of the shaft.
What are the exceptional properties of polyimide shaft liners?
Thermoset polyimide tubing can be produced in wall thickness as low as 0.0005 inches and maintained with exceptional accuracy (+/- 0.0001 inches). The finished product is a catheter tube that has outstanding burst pressure resistance, good flexibility, and a soft outer surface when a low durometer is used as the outer layer.
What medical devices, body parts or procedures are polyimide shaft liners commonly used in?
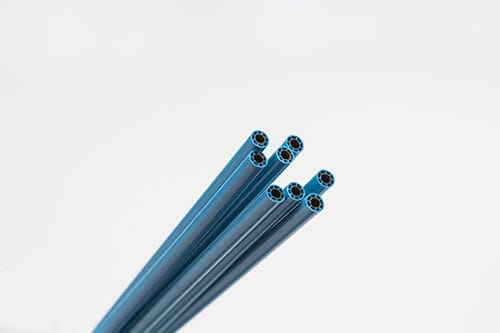
Percutaneous Transluminal Angioplasty (PTA) is a technique used to dilate an area of vascular blockage with the help of a catheter that has an inflatable small balloon at its tip.
The success of these minimally invasive procedures has accelerated the use of balloons and stents in a wide range of interventional radiology and cardiology applications. These new procedures often require reduced diameter tubes for smaller vascular openings, thinner tube walls to allow for larger lumen openings, and higher pressures for balloon and stent delivery. All of these place greater demands on the mechanical performance of the polymers used for construction.
What ISO certification does Putnam maintain?
Putnam’s leading-edge medical manufacturing facility is ISO 13485:2016 certified. Our dedicated ISO compliant cleanroom manufacturing space exceeds regulatory guidelines—so your medical device won’t be slowed by red tape.
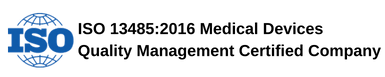
Why is Putnam the best choice for polyimide shaft lining technology?
Putnam is one of the only companies in the industry that has the capability to extrude polyimide liners into thermoplastic tubing in a continuous reel-to-reel process without using heat shrink or a reflow process. As a specialist in high-tech extrusion, Putnam can leverage over 40 years of custom manufacturing to precision engineer the best medical tubing to meet your functional requirements with the most cost-efficient material and optimal technology. You get your most demanding specifications with good speed to market and competitive rates.