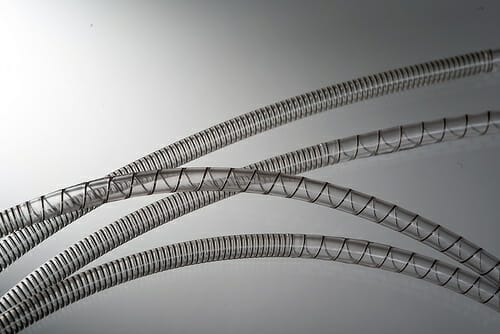
Historically, catheter designers were limited single material options along the length of the catheter. Reinforced catheters sometimes lack the required flexibility at the distal end, while unreinforced catheters sometimes lack the necessary rigidity at the proximal end.
With modern minimally invasive devices, ranging from small diameter neurovascular devices to much larger gastrointestinal devices, opposing material requirements at the distal versus proximal end of the device are becoming increasingly common.
Embedded stainless steel wire reinforcement on the proximal portion of the catheter tube improves pushabilility, torque transmission, and kink resistance upon insertion by the physician. Allowing the distal end of the same tube to remain unreinforced provides greater flexibility, optical clarity and x-ray transparency.
Previously these components have been assembled manually (‘hand lay-up assembly’) with different tubes aligned and assembled using adhesives, heat shrinking, annealling and other methods by an operator manually. This introduces considerable variation and makes it difficult to achieve a validated process. Furthermore, yields are constrained by the slow assembly process, the operator’s manual dexterity and by a lengthy annealing step.
Putnam offers custom catheter tubing with wire reinforcements embedded within the wall at the proximal end of the catheter only, and no reinforcement on the distal end. Reinforcement options include braided wire for torque transmission and coiled wire for kink resistance. These components utilize integrated extrusion, wire wrapping and welding technologies to reduce costs and improve quality over traditional hand layup methods.