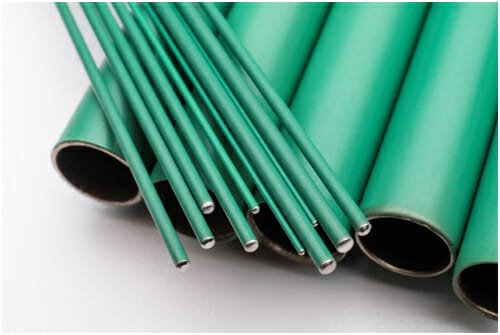
What are PTFE coating mandrels & wires?
Our PTFE coated mandrels and wires are designed to be reusable and come in various custom sizes & lengths. Discrete mandrel and continuous wire coating is compatible with a variety of metals including, but not limited to, stainless steel, silver plated copper, and Nitinol in diameters ranging from 0.010” to over 0.500” (0.254mm to 12.7mm). We can also accommodate discrete lengths up to 13 feet.
What material is used to make our mandrels & wires?
We employ a range of fluoropolymer coatings, including our proprietary RilSlix™ coating. Our RilSlix™ coating incorporates a unique surface chemistry that has been optimized for use as a processing aid in catheter manufacturing. RilSlix™ compounds have been designed with PFOA free, REACH compliant materials. All coatings are compatible with discrete, tapered and continuous wire.
Why use our coated mandrels & wires over competitors’?
Our RilSlix™ coated mandrels and wires exhibit up to 5 times stronger adhesion of the coating to the mandrel than industry standards. The RilSlix™ technology also offers unparalleled durability which enables wires/mandrels to be used repeatedly without flaking. The combination of performance, wear-resistance and longevity makes RilSlix™ coated mandrels a cost effective option, superior to standard fluoropolymer coated wires and mandrels.
What medical devices are coated mandrels & wires commonly used in?
RilSlix™ mandrels are ideal for complex multi-lumen catheters, vascular catheter, reflow processes or continuous processes where mandrels are required as they are easily released and can be used over and over again without flaking.
What ISO certifications is Putnam Plastics equipped to comply with?
Putnam’s state-of-the-art plastics extrusion manufacturing facility is ISO 13485:2016 certified.
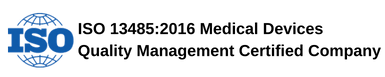
Why is Putnam Plastics the best choice for PTFE coated mandrels & wire?
Putnam has been coating wires and mandrels for nearly two decades. Our engineers are available to assist in material selection and optimization, ensuring that the polymer coating that is ultimately selected is best suited to meet specific product performance requirements. We offer in-house testing for all adhesion and coating processes. By providing both manufacturing and testing under one roof, customers benefit from a reduction in lead time and access to product design that is customer specific. Samples are also available in formats that will allow customers to evaluate bond strength, frictional properties and durability.